Anodising
the main anodising processes
Sulphuric Anodising
Sulphuric anodising or ‘normal’ anodising is used extensively for general protective and decorative applications. It produces a clear film which can be left natural or dyed to produce a range of colours, depending on the base material used. The nature of sulphuric films enables them to be used with a range of pre-treatments to produce a variety of attractive visual finishes.
Chromic Anodising
Chromic anodising is normally used for the corrosion protection of critical engineering components that require only a thin film, with minimum dimensional effect, or to ensure maximum fatigue integrity. It is also used for crack detection and is an ideal pre-treatment for paint. Chromic anodising is the preferred treatment for components containing deep crevices, since any residual electrolyte is non-corrosive to Aluminium.
Hard Anodising
Hard anodising uses formulated acid solutions normally operated at low temperatures, under high current density and voltage conditions. This produces an exceptionally hard coating with excellent wear, abrasion and corrosion resistance, and high electrical resistivity. “Hardas”, “Hardex” and “Dioxal” are variations of the hard anodising process all in use at Acorn Surface Technology, selected for use depending on the design requirements of the application. The colour of the anodic film will depend on the alloy type used as well as the process.
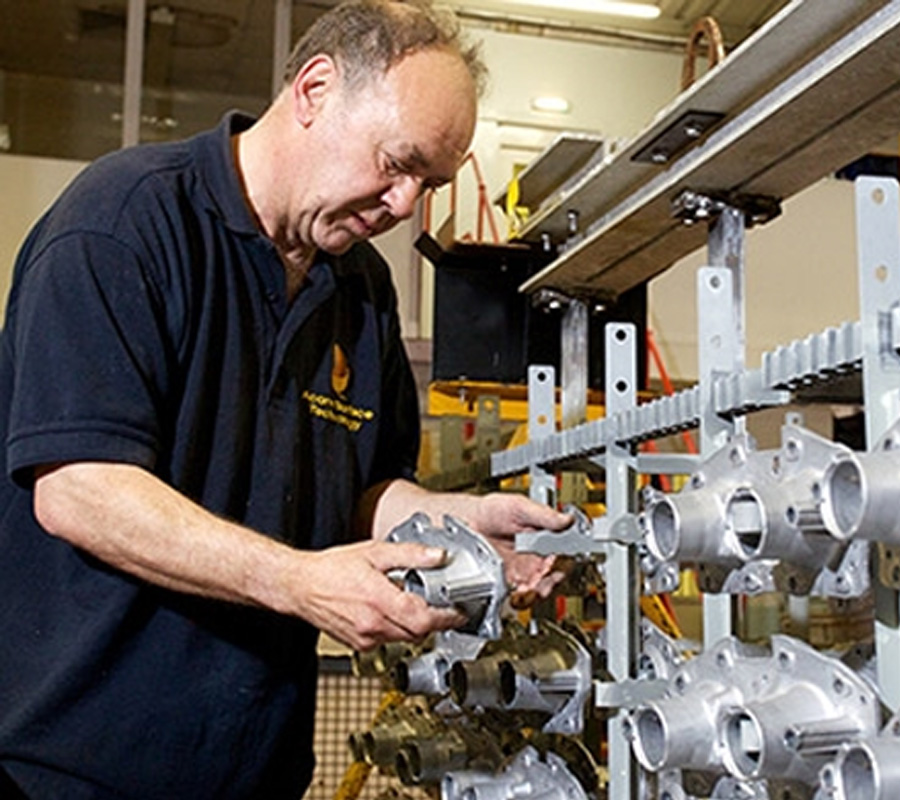
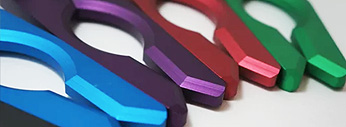
Hard anodised films are usually supplied unsealed for maximum abrasion resistance, but can be further treated with dyes, solid phase lubricants or chemically sealed for high levels of corrosion protection. By careful selection of the correct processing conditions, anodising can offer the complete answer to many Aluminium protection problems.
contact us
aalberts surface technologies OCT limited
Unit 8 • Lichfield Road Industrial Estate • Tamworth • Staffordshire • B79 7XD • United Kingdom
t :+44 (0) 1827 634 89
aalberts surface technologies limited
Clover Street • Kirkby-in-Ashfield • NG17 7LJ • United Kingdom
t: +44 (0) 1623 753 107