IVD Aluminium Coating
Vapour Deposition is a means of implementing hard surfaces, under pressure and heat, onto Aluminium and other alloys.
The manufacture of modern aircraft demands the use of high performance materials and protective systems which also need to be environmentally friendly. Historically Cadmium plating has been the mainstay for protecting both Steel and Titanium components but, following increased environmental concerns and recent legislation, it is increasingly being replaced. Many alternatives to Cadmium have been investigated over the years but none have fulfilled all the requirements, however IVD Aluminium has emerged as a single process replacement in many applications.
IVD Aluminium is a smooth, uniform coating of pure aluminium, produced by vacuum deposition and is currently used in aerospace and defence applications where critical corrosion resistance with electrical conductivity is paramount or where dissimilar metal contact can cause galvanic attack.
Typical components currently processed with an IVD Aluminium coating include – Engine and Airframe fasteners (Steel and Titanium), high tensile Steel airframe parts, Titanium bearing shells, landing gear components and assemblies, sintered magnets and electrical connectors.
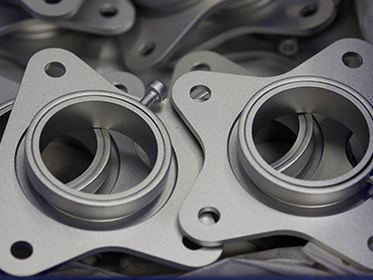
advantages
- Provides sacrificial corrosion protection to Steel without the risk of hydrogen embrittlement.
- Provides improved corrosion protection to high strength Aluminium alloys.
- Can be used in contact with aero engine fuels.
- Neither the process nor the coating create toxic materials.
- Corrosion resistance is at least equal to that of Cadmium.
- Prevents dissimilar metal corrosion e.g. Ttitanium, Stainless Steel parts in Aluminium assemblies
- The coating can be applied within closely controlled limits.
- Class 1 > 25 microns; Class 2 – 13-25 microns; Class 3 – 8-13 microns
- The coating is highly conducting.
- It is stable up to 415degC.
contact us
aalberts surface technologies limited
Clover Street • Kirkby-in-Ashfield • NG17 7LJ • United Kingdom
t: +44 (0) 1623 753 107
aalberts surface technologies OCT limited
Unit 8 • Lichfield Road Industrial Estate • Tamworth • Staffordshire • B79 7XD • United Kingdom
t :+44 (0) 1827 634 89